Written by-Christiansen Bennett
Batch pasteurization describes the procedure of preparing resources for pharmaceutical manufacturing and entails pasteurization of raw compounds in a closed vessel in such a way that the microorganisms do not run away or are destroyed by the pasteurization procedure. It is carried out for lots of sorts of pharmaceutical products such as antibiotics, analgesics, anti-carcinogens, laxatives, anti-fungal representatives, tummy prep work, and vet items. The name originates from the primary pasteurization process, where the item is run out to make sure that the organisms on its own die. The pasteurization process produces an item with nearly no preference.
"@context": "https://schema.org", "@type": "Organization", "name": "PRO Engineering / Manufacturing Inc", "url": "https://prowm.com/", "logo": "https://prowm.com/wp-content/uploads/2020/12/PRO_logo_NEW_BLK_large.jpg", "contactPoint": "@type": "ContactPoint", "telephone": "414-362-1500", "contactType": "customer service", "areaServed": ["US","PR"], "availableLanguage": "en" , "sameAs": [ "https://www.facebook.com/PartnerWithPRO", "https://twitter.com/daveone1", "https://www.youtube.com/channel/UCizF9v7dVwMEfY1Qu_E4MPg", "https://www.linkedin.com/company/pro-engineering-and-mfg-inc/", "https://soundcloud.com/pro-engineering-milwaukee" ]
In order to satisfy the standards set by the food and drug administration (FDA) for foods and also medications, makers must apply pasteurization processes as a part of the production procedure. The FDA defines a 'sterilized product' as one that undergoes any kind of among the four standard pasteurization processes: cold pasteurization, hot pasteurization, completely dry warm pasteurization, or caustic pasteurization. In fact, all pharmaceutical products might be sterilized. There is significant dispute over which of the 4 is most efficient.
Cold pasteurization is the process through which the products are warmed to decrease the development of germs during processing. The end product is typically sterilized at temperature levels below 118 degrees Fahrenheit. Heat pasteurization, on the other hand, uses an extremely heat to speed up the rate of growth of the microbes and eliminate them. Dry heat pasteurization is the least pricey of the 4 procedures, as it needs really little focus to the real problems of the ingredients throughout processing. This approach is taken into consideration the most ideal for prep work having drugs that have to undergo fast testing and also authorization before use.
Pasteurization of medicines in pharmaceutical plants has an inescapable drawback: the conservation of the drugs' residential or commercial properties. It is necessary to utilize a pure product in the prep work of these products, because any materials contributed to the products can have undesirable results on the final product. The most preferred instance is the incorporation of tinting and flavors in medication. These additives can change the chemical make-up of the drugs and also hence provide them ineffective in the treatment they are intended to cure. This is why medicines that undergo pasteurization procedures are always kept in completely dry problems as well as should be extensively mixed with an appropriate base solution.
Due to the fact that medications are themselves pure products, it is necessary to use appropriate methods of pasteurization for various kinds of items. When it comes to antibiotics, the most usual pasteurization procedure used is the supposed slow-heat treatment, which involves home heating the medicines at a temperature level below the boiling point of the water they will be provided in. This method is well fit for preparing liquids for garglings and also providing fluids having anti-bacterial agents. In the case of vaccinations, the substances made use of in the manufacturing of the items themselves are put under pressure in a container, and after that enabled to cool down to space temperature level. The slow-heat pasteurization procedure employed during the manufacturing of syrups and also other medicines that are to be consumed by mouth is referred to as the increased pasteurization process.
https://www.wattagnet.com/blogs/14-food-safety-and-processing-perspective/post/38219-new-approach-for-table-egg-pasteurization-in-development of the most typically made use of basic materials in the pasteurization procedure utilized in medication manufacture are alcohols and also denatured alcohols, in addition to xylene, chloroform, and also various other strong synthetic chemicals.
https://qz.com/740959/science-has-found-a-way-to-extend-the-shelf-life-of-cold-milk-300/ as materials, solvents, barrier solutions, or surfactants may also be used. These substances should undergo several stages of pasteurization, from their introduction to the last temperature level at which they are contributed to the item. Usually, the duration of pasteurization in the manufacture of a product ranges between five to fifteen minutes, although this depends considerably on the type of compound involved.
Throughout the last of the pasteurization process, a particular rate needs to be fulfilled in order to maintain the temperature of the product listed below boiling. In general, it takes about ten mins for the pasteurization of any kind of strong compound at an offered temperature to occur. Solids that take longer to steam include solutions, which are mainly utilized to emulsify and also blend ingredients in pharmaceuticals; thermoset compounds, such as polyols and monomer particulates utilized as providers in printing devices; and also volatile natural compounds (VOCs), which are by-products generated during the process of alcohol distillation. Some medicines are heavily loaded with VOCs, and they have to be dealt with separately.
A typical procedure making use of Tunnel pasteurization includes a series of actions. Initially, the alcohols and other chemical compounds are warmed to regarding 100 degrees Celsius, at which point they are introduced to the injector, which supplies a constant flow of hot injector gas throughout the item's manufacture. Next, the alcohols are pelletized and after that taken right into a chamber where they remain for numerous hours. Lastly, they are drained pipes of the majority of their solutes, and their deposit collected after a last dose of shot. The quantity of solute gotten rid of differs by chemical type and also set; products are generally examined before each set, to guarantee that all chemical constituents have actually been efficiently gotten rid of.
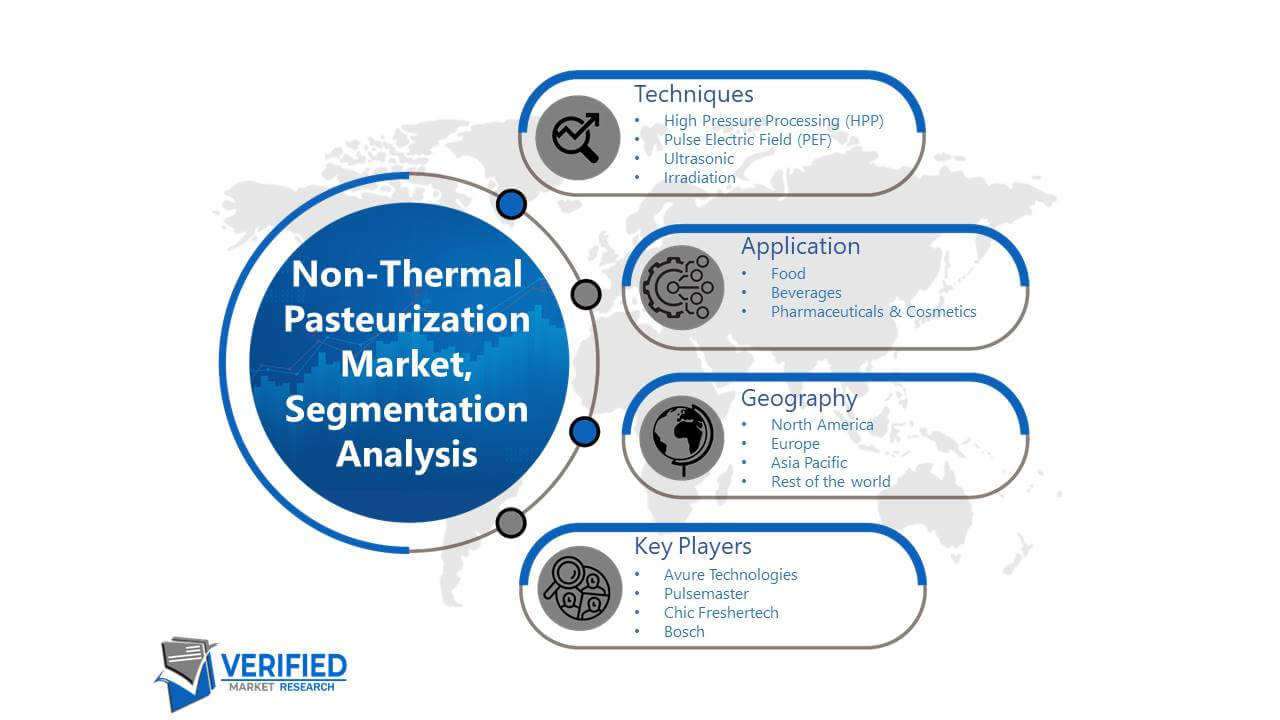